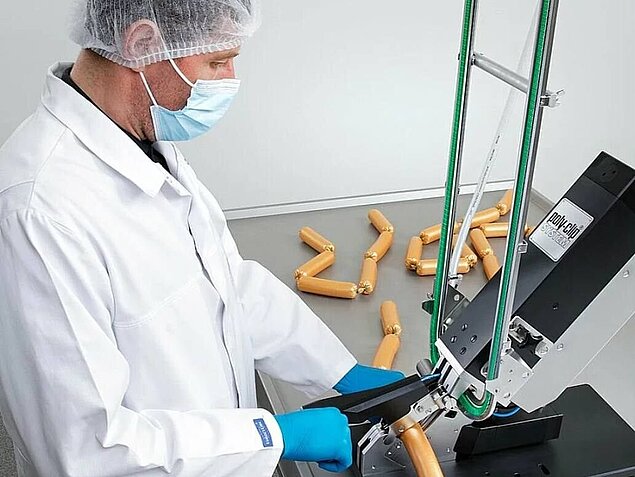
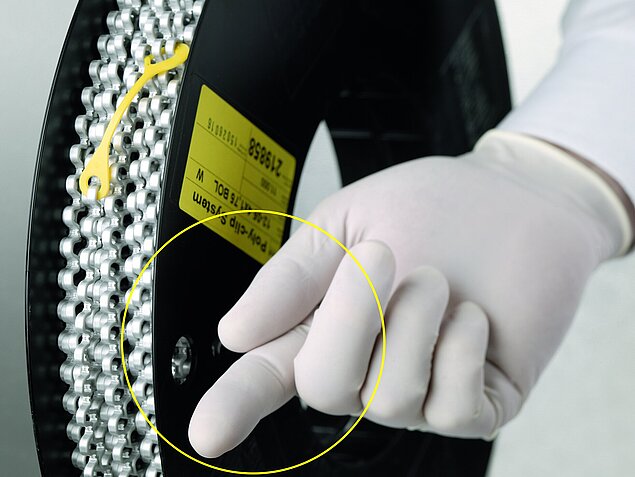
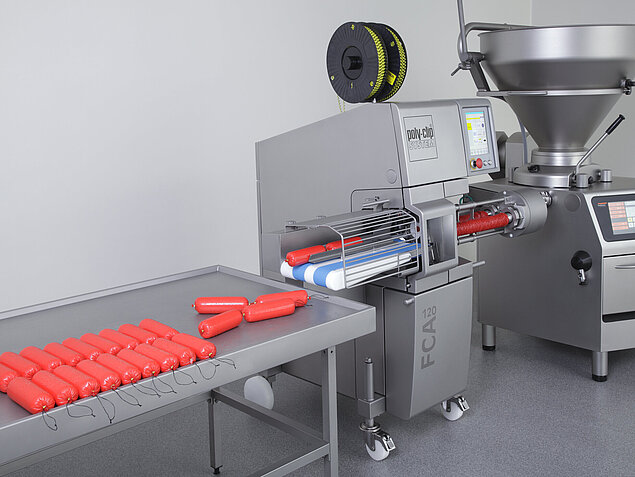
The Right Decision Starts Here: A Guide to Choosing Your Ideal Clipper
In packaging operations, a clipper is more than just a machine — it's a key part of your production line. The right choice directly impacts waste, productivity, maintenance costs, and your ability to meet production goals. A rushed decision can lead to bottlenecks, unexpected expenses, or underused equipment.
This guide will help you choose the right clipper, anticipate common issues, and understand what to expect from advanced systems like Poly‑clip machines.
1. Scale According to Your Actual Production
Oversized machines: high investment, low utilization.
Undersized machines: slow processing, bottlenecks, lower efficiency.
The key is to assess your current and projected volume to select a machine that truly supports your operations.
2. Clipping Pressure and Clip Type Matter
L clips: require low pressure (< 6 bar), ideal for rigid casings.
S clips: work at higher pressure (up to 6 bar) with excellent precision, ideal for soft or thin casings.
Using the wrong clip can stretch the casing excessively, causing tearing, poor seals, and unnecessary waste.
3. Matrices: Protect the Core Component
Matrices are the heart of the clipping process. If they're misaligned or made of low-quality materials, they wear out quickly — causing unplanned downtime and high maintenance costs.
4. Separator Knives: Precision Depends on the Angle
Improper angles in separator knives lead to defective cuts, casing damage, and excessive wear. Precise calibration and trained operators ensure optimal performance.
5. Don’t Overlook Clip–Casing Compatibility
When your development team introduces new recipes, they often skip compatibility checks between the clipper, clips, and new casings. This can lead to jams, production stops, or the need to replace machines mid-process.
6. Common Issues and How to Prevent Them
Issue | Common Cause | Impact | Strategic Solution |
---|---|---|---|
Overstretched casing | Wrong clip/pressure | Product damage, increased waste | Match clip and pressure to casing type |
Worn-out matrices | Friction, poor materials | Downtime, costly repairs | Use durable materials and calibrate regularly |
Misaligned separator knives | Incorrect angles | Defective cuts, excessive wear | Proper knife angle adjustment and routine maintenance |
Slow clipping speed | Undersized machine | Bottlenecks | Match machine capacity to production volume |
Underused machine | Oversized equipment | Inefficient capital use | Select based on real production demands |
Clip/casing incompatibility | Lack of product–equipment validation | Operational failure | Test every new casing with the actual clipper and clips |
7. Maintenance: Your Best Long-Term Investment
Most operational issues come from poor lubrication, improper cleaning, and worn parts. A preventive maintenance plan with regular inspections, timely part replacements, and cleaning routines extends machine life and keeps efficiency high.
8. Poly‑clip Clippers: High Performance and Food Safety in One Solution
In food production, reliability and hygiene are non-negotiable. Poly‑clip machines are built to meet the most stringent industry standards and offer several advantages:
Hygienic design: stainless steel construction, smooth surfaces, and easy access for deep and fast cleaning.
Food-safe clips: oil- and grease-free, made from certified materials with full traceability.
Operational efficiency: precise closure systems ensure consistent seals and reduce product waste.
Automation-ready: technologies like RFID enable advanced control, batch tracking, and integration into smart production lines.
Low maintenance: durable components, minimal wear, and fast replacement of key parts to prevent unplanned downtime.
These features make Poly‑clip a trusted name in the food industry — offering reliability, hygiene, and continuous output.
Conclusion
Choosing the right clipper directly affects your line’s efficiency, food safety standards, and cost control.
In the food industry, where regulations are strict and product consistency is crucial, you need a machine that delivers precision, hygiene, and durability. Take time to assess your real volume, validate your clips and casings, calibrate key parts, and implement preventive maintenance.
With solutions like Poly‑clip, you're investing in proven technology designed for the demands of modern food production: less waste, maximum hygiene, and consistent output.
Want to assess your current line or explore which models fit your process best? I'm here to help you make the right choice.